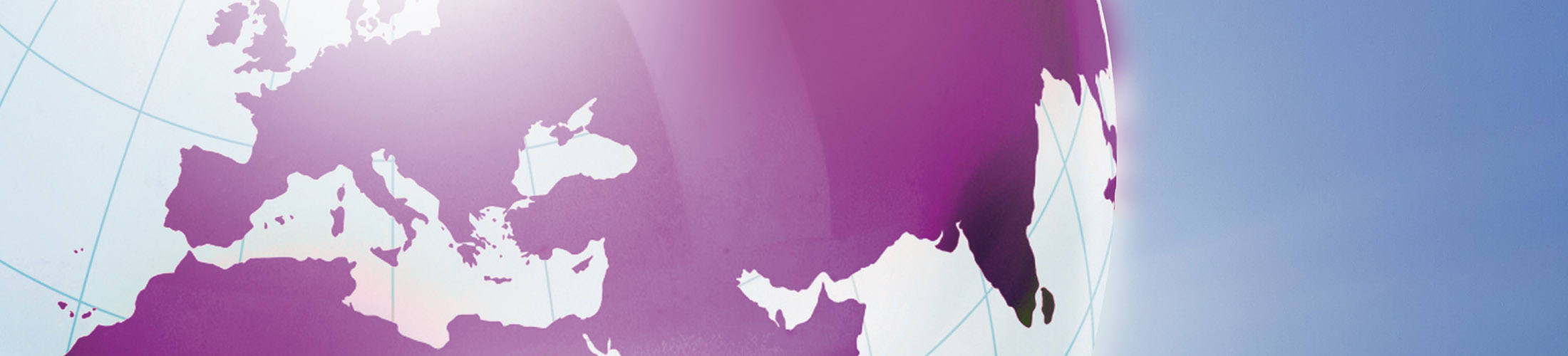
按行业分
- 涂料
- 建筑涂料 水性木器漆 印铁涂料 印花胶浆 纸张涂料
- 油墨
- 纸张油墨 塑料油墨 纸张光油 扑克光油 烟包光油 啤酒箱光油 水性磨光油 水性哑光油
- 皮革
- 皮革涂饰剂 鞋化 鞋乳 鞋底
- 纺织
- 水性粘胶剂
- 金属加工/水性脱模剂
- 地板
- 石材地板 实木地板 PVC地板
- 食品包装用纸
- 玻璃纤维
- 建材
超高浓度石蜡乳状液的研制
超高浓度石蜡乳状液的研制
蒋金芝,阎智勇(中南大学化学化工学院,湖南 长沙 410083)
摘 要:超高浓度石蜡乳液,是蜡含量能达到 50%的同时具有良好流动性、高度分散性和稳定性等特点的白色乳
液。本文以工业石蜡为主要原料,采用特殊工艺和新型复配乳化剂,最终制得了环保型超高浓度石蜡乳液。考察
了乳化剂的选择及其用量、新型复配乳化剂中各组分的比例、乳化温度、乳化时间和搅拌速度对石蜡乳化效果的
影响。并确定了较佳乳化工艺条件:新型复配乳化剂为 7%(以总固含量为基准的质量分数),乳化时间 40 min,
乳化温度为 70 ℃,搅拌速度 1700 r/ min。在此条件下,石蜡乳液蜡含量为 50%,且稳定性、分散性、流动性较好。
关性词:石蜡乳液;浓缩乳化;乳化剂
中图分类号:TQ 423 文献标识码:A 中图分类号:1000–6613(2008)10–1632–05
石蜡乳液又叫乳化蜡,是固体石蜡均匀分散在水 中的乳液;其使用时无需加热熔融或用溶剂溶解,成 膜均匀、覆盖性好,且易于和其它物质的水溶液或乳 液复合使用,具有安全、高效和经济环保等优点 [1] , 是一种用途广泛的化工产品。一般低浓度的乳化蜡的 用途如下:医药行业上用作乳胶制品的助剂;农业上 用作果品保鲜等。而高浓度乳化蜡,蜡含量一般为 35%,由于其蜡含量更高,覆盖性更好,相应使用成 本更低,应用范围更为广泛,如在建筑行业上用作钢 筋混凝土的固化剂;造纸工业上用作纸浆施胶剂;印 刷油墨中作分散剂;皮革行业中用作涂饰剂等 [2 - 3] 。
乳化蜡最早是美孚石油公司在20世纪50年代开始研究开发,10 年后即已在美国普遍使用。20 世纪 70 年代时,英国、联邦德国、日本也逐渐开始研究 和应用乳化蜡 [4] 。目前,国外已有专利 [5 - 7] 报道了蜡 含量不低于 50%的石蜡乳液。我国该方面研究起步较 晚,目前其开发应用与国外相比差距很大,需使用乳 化蜡的部门几乎全用不合理的代替品,而且研究及生 产出的乳白色、高浓度的乳化蜡品种更是极少。 石蜡乳液的制备按照乳化剂的加入方式,一般 分为 4 种 [8] :剂在水中法、剂在油中法、初生皂法、轮流加液法等。本工作的实验证明这 4 种方法均难 以得到浓度超过 35%、且具有良好流动性的高浓度 石蜡乳液。因此,本工作分别对石蜡乳化剂的选择、 乳化条件的影响、乳化工艺的改进进行探讨,拟研 究出新型复配乳化剂,并采用特殊工艺,获得国内 尚未见报道的超高浓度石蜡乳液,其蜡含量可达 50%,并为石蜡乳液产品的多用途开发研究和应用 提供可靠的实验数据。
1 实验部分
1.1 石蜡乳化原理
石蜡乳液是一种热力学不稳定体系,放置时石 蜡和水两相易分离。要使石蜡分散于水中成为高分 散、均匀、稳定的乳液,必须选择合适的乳化剂并 通过一定的乳化工艺来实现。乳化剂使石蜡固体形 成微小的液滴(粒径在 1~3 µm)并能定向吸附其 表面,使石蜡水界面形成具有一定机械强度的界面 膜,从而使稳定分散于水中而不易聚结析出。因此 要制得颗粒细小、均匀稳定的石蜡,乳化剂的选择 是首要条件 [9] ,其次是乳化的工艺及条件。
一般浓度乳化蜡液的制备由于蜡含量低,采用 一般工艺和两种乳化剂复配便可得到机械强度足够 的界面膜;而高浓乳化蜡液由于蜡含量高,若乳化 剂在乳液粒子表面形成的吸附层不够致密,界面膜 强度低,将导致乳粒相互靠拢合并成大颗粒而破乳 分层。因此制备超高浓乳化蜡液的关键在于找出新 乳化剂以在石蜡水界面得到足够强度的界面膜。
1.2 仪器及药品
仪器:电炉(1000 W)、恒温电磁搅拌水浴锅、 锥形瓶。
药品:45 # 石蜡(工业级)、硬脂酸(分析纯)、 乳化稳定剂 HP-1(工业级)、助剂 AP-2(分析纯)、 助剂 AP-1(工业级)。
1.3 制备方法
本实验采用浓缩乳化再稀释的特殊工艺,具体 操作如下。
将 25 g 工业石蜡、11 g 水、0.085 g 乳化稳定剂 HP-1、1.24 g 硬脂酸、0.085 g 助剂 AP-1 在烧杯中 混合并薄膜密封,用电炉加热直至蜡固体开始融化, 再移至水浴温度为 70~72 ℃的水浴锅中。待固体 全部融化后,先将瓶内液体搅拌均匀,此时呈略黄 的乳白色,再向其中加入 0.49 g 助剂 AP-2,搅拌均 匀,并在瓶内 70 ℃下搅拌 40 min,搅拌速率为 1700 r/ min。冷却并搅拌,直至瓶内温度降为 35~38 ℃此时再向瓶中加入 12 g 50~55 ℃的自来水进行稀 释,最后边搅拌边冷却至室温。
1.4 乳化蜡性能测试方法
文中乳化蜡性能的测试均在蜡含量为 50%的 石蜡乳液中进行。
1.4.1 稳定性测定 将乳化蜡在室温下静置 30 天后,测量乳化液的 体积(V O )占整个溶液体积(V T )的分数,其值越 大,表明所制备的乳化液越稳定。
1.4.2 分散性检测 分散性测定参照农乳的 5 个等级,一级较好, 五级最差,具体见文献[10]。
1.4.3 石蜡乳液类型评定 采用冲淡法。取少许石蜡乳液,加入少量水, 轻轻搅拌,易与水掺合者为水包油型(O/W),反 之,为油包水型(W/O)。
2 结果与讨论
2.1 乳化剂的选择及其用量的确定
2.1.1 乳化剂的选择 选择乳化剂通常以亲水-亲油平衡值(HLB) 为依据,石蜡乳化要求 HLB 值在 10 左右,而且经 验表明,乳化蜡的稳定体系需要两种以上的表面活 性剂才有较好的效果 [11] 。为此,可以利用有机概念 图,图中将有机物亲油和亲水的程度用数字来表示, 即有机性值(O)和无机性值(I)。这样就能根据 化合物的有机性值辅助选择乳化剂 [12 - 14] 进行复配, 即利用了有机性值相近相溶原则选择乳化剂。
石蜡的 O 值范围为 520~640。几种乳化剂的有 机性值和无机性值见表 1。
由表 1 中各乳化剂的 I、O 值,可知用助剂 AP-2 与硬脂酸复配的乳化剂较好。在此基础上,通过查 阅相关资料 [15] ,又加入乳化稳定剂和助剂 AP-1 再进 行复配得到新型复配乳化剂,并通过实验考察了不同复配乳化剂对石蜡乳液稳定性的影响(本文中每 次实验的总质量均规定约为 50 g,其中石蜡为 25 g, 水为 23 g,各类助剂共 1.9 g)。实验结果如表 2。
从表 2 可知,4 种乳化剂复配的新乳化剂能得 到具有流动性的高含量石蜡乳液。因此,选用硬脂 酸、乳化稳定剂 HP-1、助剂 AP-2、助剂 AP-1 进行 复配得到新型复配乳化剂。
2.1.2 乳化剂用量的选择
实验已证明表面活性剂作为乳化剂时,其在界 面上形成吸附膜的强度与界面活性剂的浓度有 关 [16] ,因此只有加入足够量的乳化剂才能达到较佳 乳化效果。但乳化剂用量过多,产品会形成太多气 泡而影响其质量。因此乳化剂一般遵循采用必不可 少的最低用量原则,通常为总固含量的 4%~15%。 通过实验考察了不同用量的上述新型复配乳化剂对 石蜡乳化效果的影响,结果见表 3(本文中“-” 表示乳液凝固无法评价)。
从表 3 中可知,当新型复配乳化剂用量小于 6% 时,无法得到具有流动性的高浓度乳化液;用量大 于 7%时,石蜡乳化效果即较好,但为避免产生太 多气泡以及提高成本,选取乳液总固含量的 7%为 新型乳化剂的含量。
2.1.3 乳化剂中各组分间比例的确定
由表1和文献[17]知硬脂酸和助剂AP-2应为乳 化剂中主要成分,且它们质量之和与乳化稳定剂 HP-1 和助剂 AP-1 质量之和的比应约为 1∶10。为 探讨乳化剂组分间的比例问题,先固定乳化稳定剂 HP-1 和助剂 AP-1 的用量,将硬脂酸与助剂 AP-2 按不同比例进行实验,考察其对石蜡乳液稳定性的 影响,结果见表 4。
由表 4 可知,硬脂酸过量,可使乳化蜡的稳定 性增强。这是因为硬脂酸具有较小的亲水端基,能 有效吸附在界面上和插入表面活性剂分子之间,呈 更紧密的空间排列,形成致密的高强度膜。但硬脂 酸过量太多反而影响乳液的稳定性,因此我们确定 硬脂酸和助剂 AP-2 的比大约为 2.5∶1。
其次在表 4 中 5 号实验的基础上,考察乳化稳 定剂HP-1和助剂AP-1两者之间的比例对乳化蜡稳 定性的影响,结果如表 5 所示。
由表 5 可知,乳化稳定剂 HP-1 和助剂 AP-1 的 较佳比例应为 1∶1。
根据乳化剂的总量约为 1.9 g,可计算得出上述 较佳比例下新型乳化剂中的各成分的质量分别为: 1.24 g 硬脂酸、0.49 g 助剂 AP-2、0.085g 乳化稳定 剂 HP-1、0.085 g 助剂 AP-1,其在乳液中的质量分 数分别为 2.48%的硬脂酸、0.98%的助剂 AP-2、 0.17%的乳化稳定剂 HP-1、0.17%的助剂 AP-1。
2.3 乳化温度的影响
适宜的乳化温度可以使蜡微粒在搅拌作用下迅速而充分地分散,增加乳液的稳定性。温度对石蜡乳液的影响见表 6。
从表 6 中可看出,温度低于 70 ℃时,难以得 到稳定的石蜡乳液,因此乳化温度应不低于 70 ℃, 最终选取 70 ℃。
2.4 乳化时间的影响
在较佳乳化剂用量以及乳化温度的条下,考察了乳化时间对石蜡乳液的稳定性的影响,实验结果如表 7 所示。
由表 7 可见,乳化时间太短石蜡不能充分乳化,时间太长则造成浪费。实验证明乳液粒径开始时随时间的延长而变小,但一定时间后粒径不再变化。乳化时间超过40 min,即可得到稳定的石蜡乳化液。因此我们选择较佳乳化时间为 40 min。
2.5 搅拌速度的影响
杨基和等 [18] 发现,在乳化过程中,搅拌速度也会影响石蜡乳液的性质。速度过低不能将油相的蜡较好的乳化,乳液颗粒不均匀;搅拌速度过高,则易带入大量的气泡,消泡困难,并且搅拌速率太高会使乳化蜡破乳,影响其稳定性。不同的搅拌速率对乳化液的影响见表 8。
从表 8 中可见,搅拌速率大于 1500 r/min 时,乳液稳定性和分散性较好,但搅拌速率过快则不宜控制,且能耗较高。而当搅拌速率低于 500 r/min时则难以得到石蜡乳液。因此选择 1700 r/min 为合适的搅拌速率。
2.5 新型乳化工艺
石蜡乳液的制备常采用剂在水中法、剂在油中法和初生皂法等。在确定了上述新型复配乳化剂后,在保证 50%蜡含量的前提下,通过实验进行了传统乳化工艺和新工艺的对比研究,实验结果见表 9。
由表 9 可知,传统的 3 类方法均难以制得有流动性的蜡含量为 50%的高浓度石蜡乳液,而采用新工艺,不仅可以简化制作条件,也能得到具有流动性的高浓度乳化液。
2.6 产品性能
制得的超高浓度石蜡乳液基本无毒,符合环保要求,外观为乳白色,经检测为 O/W 型,分散性为二级,稳定放置 40 天不分层。
3 结 论
(1)确定了新型复配乳化剂及其配方(质量分数):乳化稳定剂 HP-1 为 0.17%,助剂 AP-2 为0.17%,助剂 AP-1 为 0.98%,硬脂酸为 2.48%。(2)研究出了将水油初始混合进行浓缩乳化,然后再稀释的新石蜡乳化工艺,并对乳化工艺条件进行考察,确定了制备稳定石蜡乳液的较佳工艺条件为:乳化温度 70 ℃,乳化时间 40 min,搅拌速度 1700 r/min。
(3)制得了蜡含量高达 50%的超高浓度石蜡乳液,且其流动性、稳定性和分散性均较好。
(4)本方法所需生产设备及原料简单,工艺条件易于操作,产品经济环保,适于工业化生产。
本文超高浓度石蜡乳状液的研制内容经过编辑,如无授权,请勿拷贝。 如果您对超高浓度石蜡乳状液的研制感兴趣可以联系我们 18566398802
有机硅憎水剂提升建筑外墙瓷砖防水性能的核心,在于其特有的化学性质与物理作用。首先,其分子中的硅醇基与瓷砖、混凝土等硅酸盐材料的硅醇基发生脱水交联反应,在墙面形成憎水层。该层使水滴接触后难以渗入,自然滑落,通过“反毛细管效应”显著增强防水性。其次,有机硅憎水剂具备微膨胀与增密功能。涂覆后渗透至基层微孔中膨胀,封闭孔隙以提高密实度,从而强化防水效果。此外,其形成的防水层兼具优异透气性与耐候性。既保障墙
液体石蜡的乳化研究段月英1,丛玉凤1,黄 玮1,赵红丽1,唐 东1,白双福1,郭金鹏2,高 瞩1(1.辽宁石油化工大学,辽宁 抚顺113001;2.辽河油田特种油开发公司,辽宁 盘锦124000)摘 要: 以液体石蜡为原料,采用添加助剂的方法,制备了石蜡乳液。探讨了乳化剂种类及其质量分数、乳化水质量分数、乳化温度、乳化时间等因素对乳化效果的影响。结果表明,复配乳化剂乳化效果较好,各因素对乳化效果的
非离子型石蜡乳液的制备江金龙,黄铃(湖南化工职业技术学院,湖南 株洲 412004)[摘 要]以 58#石蜡和复配乳化剂为原料,采用剂在油中法,制备了非离子石蜡乳液。考察了乳化剂类型、乳化剂用量、乳化温度、乳化时间、搅拌速度对石蜡乳液性能的影响。确定了较佳乳化工艺条件:复配乳化剂用量 9 %,乳化温度 85 ℃,乳化时间 40 min,搅拌速度 500 r/min。成品含固量约为 30 %,具有良
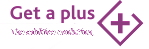
佛山市翁开尔贸易有限公司 WebSite 粤ICP备05045526号公安机关备案号44060402000074号 网站地图